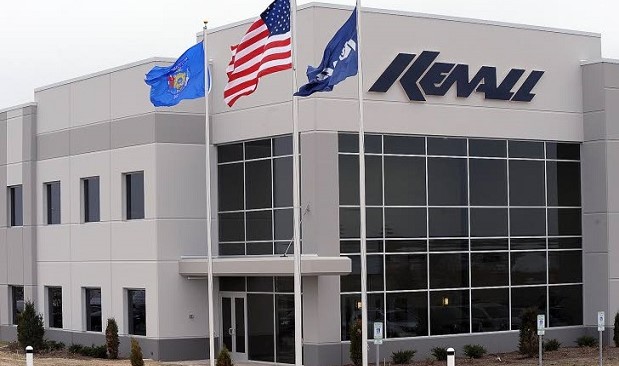
CHICAGO—Manufacturing has undergone several changes since the advent of the recession, and those changes could end up benefitting many areas once considered off the beaten path. At a time when many businesses are flocking to the nation's downtown cores, manufacturers are headed in the opposite direction.
“The first and most important thing to these companies is access to low- and no-skilled labor,” Thomas Boyle, Chicago-based principal with Transwestern, tells GlobeSt.com, especially ones that need seasonal labor. “Not having that access hurts their operating expenses.”
But that access to labor has to be coupled with affordable land costs, affordable energy, and great transportation networks that can move products from the manufacturing site to the customers, and that combination only exists in certain pockets of the Chicago metro area and the greater Midwest, adds the site selection expert.
With land costs hitting record highs in dense markets such as O'Hare, that means many companies are taking peeks at these “overlooked areas,” says Boyle. “It's the inverse of what is happening in the office sector.”
And to bring manufacturing operations to once-overlooked areas, the competition can get intense, Boyle says. He recently helped Kenall Manufacturing, a commercial lighting company, relocate its headquarters and factory from north suburban Gurnee, IL, to a facility just over the WI border in Kenosha. Like many firms in the area, it needed to expand, but company officials wanted to preserve the workforce they had recruited, restricting possible locations to northeastern IL or southeastern WI.
“We negotiated a significant municipal incentives package,” says Boyle, and that helped tip the balance to Kenosha, after starting with 25 to 30 feasible locations. The move allowed Kenall to expand from a 120,000-square-foot building to a 354,000-square-foot facility in the Business Park of Kenosha. “One of the things I do most is move companies from Illinois to Wisconsin.”
A big factor that is helping US manufacturers expand is the intensifying demand from customers for quick delivery. That means more products have to be made in the US, as companies “don't have ten weeks to wait for the boat to get here,” says Boyle. And that desire from customers can help fuel even more jobs expansion. “Every manufacturing job creates three other jobs,” including some in the many new logistics and distribution buildings springing up across the US.
Towns primed to benefit from manufacturers' current needs include those on the periphery of metro areas such as Waukegan, IL, a far north suburb of Chicago near the WI border; Valparaiso, IN; and South Milwaukee, among others. “You can't go too rural; the workers just aren't there,” says Boyle.
But communities that really want to be successful at attracting new manufacturing facilities also need to think about providing education to those existing labor pools, alongside the incentives and affordable land. Boyle says, for example, that Gateway Technical College, which has several campuses in southeastern WI, including one in Kenosha, has become an important source of skilled labor and customized training for Kenall and several other local companies.
In fact, during the site selection process, Boyle's team works with local community colleges like Gateway to design courses that will prepare future employees for the jobs headed their way. “Not everyone needs to graduate with a liberal arts degree.”
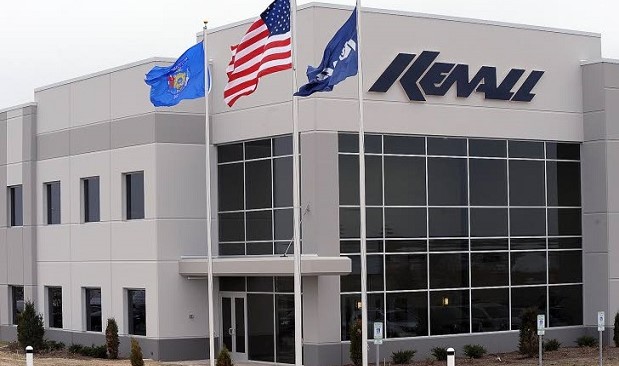
CHICAGO—Manufacturing has undergone several changes since the advent of the recession, and those changes could end up benefitting many areas once considered off the beaten path. At a time when many businesses are flocking to the nation's downtown cores, manufacturers are headed in the opposite direction.
“The first and most important thing to these companies is access to low- and no-skilled labor,” Thomas Boyle, Chicago-based principal with Transwestern, tells GlobeSt.com, especially ones that need seasonal labor. “Not having that access hurts their operating expenses.”
But that access to labor has to be coupled with affordable land costs, affordable energy, and great transportation networks that can move products from the manufacturing site to the customers, and that combination only exists in certain pockets of the Chicago metro area and the greater Midwest, adds the site selection expert.
With land costs hitting record highs in dense markets such as O'Hare, that means many companies are taking peeks at these “overlooked areas,” says Boyle. “It's the inverse of what is happening in the office sector.”
And to bring manufacturing operations to once-overlooked areas, the competition can get intense, Boyle says. He recently helped Kenall Manufacturing, a commercial lighting company, relocate its headquarters and factory from north suburban Gurnee, IL, to a facility just over the WI border in Kenosha. Like many firms in the area, it needed to expand, but company officials wanted to preserve the workforce they had recruited, restricting possible locations to northeastern IL or southeastern WI.
“We negotiated a significant municipal incentives package,” says Boyle, and that helped tip the balance to Kenosha, after starting with 25 to 30 feasible locations. The move allowed Kenall to expand from a 120,000-square-foot building to a 354,000-square-foot facility in the Business Park of Kenosha. “One of the things I do most is move companies from Illinois to Wisconsin.”
A big factor that is helping US manufacturers expand is the intensifying demand from customers for quick delivery. That means more products have to be made in the US, as companies “don't have ten weeks to wait for the boat to get here,” says Boyle. And that desire from customers can help fuel even more jobs expansion. “Every manufacturing job creates three other jobs,” including some in the many new logistics and distribution buildings springing up across the US.
Towns primed to benefit from manufacturers' current needs include those on the periphery of metro areas such as Waukegan, IL, a far north suburb of Chicago near the WI border; Valparaiso, IN; and South Milwaukee, among others. “You can't go too rural; the workers just aren't there,” says Boyle.
But communities that really want to be successful at attracting new manufacturing facilities also need to think about providing education to those existing labor pools, alongside the incentives and affordable land. Boyle says, for example, that Gateway Technical College, which has several campuses in southeastern WI, including one in Kenosha, has become an important source of skilled labor and customized training for Kenall and several other local companies.
In fact, during the site selection process, Boyle's team works with local community colleges like Gateway to design courses that will prepare future employees for the jobs headed their way. “Not everyone needs to graduate with a liberal arts degree.”
© Touchpoint Markets, All Rights Reserved. Request academic re-use from www.copyright.com. All other uses, submit a request to [email protected]. For more inforrmation visit Asset & Logo Licensing.