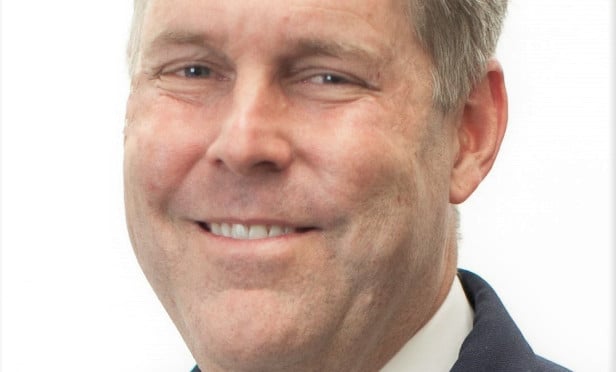
SAN DIEGO—Lack of quality control and assurance in manufacturing is leading to a major crisis in CRE construction, caused by damaged goods, late deliveries and other issues, Bingham Construction's CEO Jeff Bingham tells GlobeSt.com. Bingham says suppliers to the construction industry are becoming overwhelmed with orders and are unable to handle them properly, which is costing contractors like him money and, potentially, clients. Bingham spoke with us exclusively about this issue and what he believes should be done about it.
GlobeSt.com: How is the growth of manufacturing and commerce affecting the construction industry?
Bingham: Over the past few years, I have witnessed a significant increase in material-delivery issues resulting from damaged or incorrect materials received and orders that were either placed incorrectly or not at all. Logistics firms are also struggling with quality-control issues such as traffic accidents involving their equipment, goods damaged in transit, or materials being lost all together or shipped to the wrong address. In addition, the logistics employees don't seem to care when they arrive to a job site, where they park their vehicle, if they leave any trash or debris behind or if they should contact the contact person on the delivery to advise that it has arrived.
GlobeSt.com: Can you provide examples of how manufacturing and commerce is negatively affecting your business?
Bingham: Some of the most recent examples I can share include carpet tile that was shipped with corners bent and multiple dye-lots, light fixtures with cracked lenses or no lens at all, HVAC units with the wrong voltage, refrigerators with dents in the doors, wrong color paint, back-ordered doors, doors that were shipped with the wrong hardware prep three times and factories that have shut down due to adverse weather conditions. In the world of commercial tenant improvements, we're on the clock to deliver the tenant's new office space as quickly and efficiently as possible. No one can afford to add schedule float time or extended general-condition costs to already razor-thin project margins and deadlines to cover a manufacturer's inability to produce the correct or non-damaged product.
GlobeSt.com: What can a manufacturer or logistics firm do to mitigate these issues impacting the construction industry?
Bingham: Manufacturers and logistics firms need to bring back the quality control and quality assurance jobs that were lost during the recession.
GlobeSt.com: How are manufacturing and commerce issues changing the way you work on a project?
Bingham: The manufacturers and logistics companies rarely take responsibility for their actions and attempt to right their wrongs. When they do, the manufacturers will replace their damaged or incorrect materials at their cost. However, if you've waited six weeks for light fixtures and some of them were damaged, you'll have to wait another six weeks to get replacements, and they certainly will not compensate you for lost time waiting for new product. All the while, your tenant may be moving in within the next two weeks, and you are now forced to come up with an alternate fixture to get through final inspections and allow the tenant to move in per the original schedule. If you receive a boxed item from a logistics company, unless you remove the packaging and report any deficiencies to the driver immediately, you end up accepting responsibility for the damaged good(s) by signing for them.
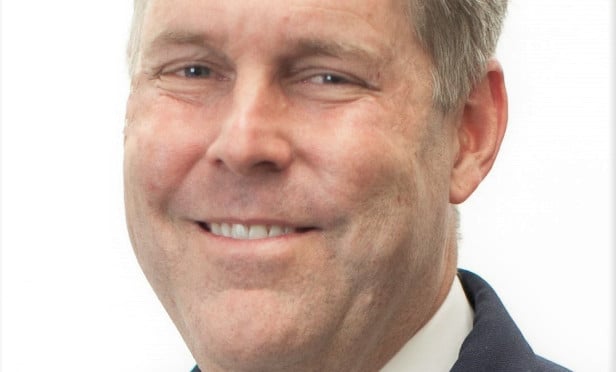
SAN DIEGO—Lack of quality control and assurance in manufacturing is leading to a major crisis in CRE construction, caused by damaged goods, late deliveries and other issues, Bingham Construction's CEO Jeff Bingham tells GlobeSt.com. Bingham says suppliers to the construction industry are becoming overwhelmed with orders and are unable to handle them properly, which is costing contractors like him money and, potentially, clients. Bingham spoke with us exclusively about this issue and what he believes should be done about it.
GlobeSt.com: How is the growth of manufacturing and commerce affecting the construction industry?
Bingham: Over the past few years, I have witnessed a significant increase in material-delivery issues resulting from damaged or incorrect materials received and orders that were either placed incorrectly or not at all. Logistics firms are also struggling with quality-control issues such as traffic accidents involving their equipment, goods damaged in transit, or materials being lost all together or shipped to the wrong address. In addition, the logistics employees don't seem to care when they arrive to a job site, where they park their vehicle, if they leave any trash or debris behind or if they should contact the contact person on the delivery to advise that it has arrived.
GlobeSt.com: Can you provide examples of how manufacturing and commerce is negatively affecting your business?
Bingham: Some of the most recent examples I can share include carpet tile that was shipped with corners bent and multiple dye-lots, light fixtures with cracked lenses or no lens at all, HVAC units with the wrong voltage, refrigerators with dents in the doors, wrong color paint, back-ordered doors, doors that were shipped with the wrong hardware prep three times and factories that have shut down due to adverse weather conditions. In the world of commercial tenant improvements, we're on the clock to deliver the tenant's new office space as quickly and efficiently as possible. No one can afford to add schedule float time or extended general-condition costs to already razor-thin project margins and deadlines to cover a manufacturer's inability to produce the correct or non-damaged product.
GlobeSt.com: What can a manufacturer or logistics firm do to mitigate these issues impacting the construction industry?
Bingham: Manufacturers and logistics firms need to bring back the quality control and quality assurance jobs that were lost during the recession.
GlobeSt.com: How are manufacturing and commerce issues changing the way you work on a project?
Bingham: The manufacturers and logistics companies rarely take responsibility for their actions and attempt to right their wrongs. When they do, the manufacturers will replace their damaged or incorrect materials at their cost. However, if you've waited six weeks for light fixtures and some of them were damaged, you'll have to wait another six weeks to get replacements, and they certainly will not compensate you for lost time waiting for new product. All the while, your tenant may be moving in within the next two weeks, and you are now forced to come up with an alternate fixture to get through final inspections and allow the tenant to move in per the original schedule. If you receive a boxed item from a logistics company, unless you remove the packaging and report any deficiencies to the driver immediately, you end up accepting responsibility for the damaged good(s) by signing for them.
© Touchpoint Markets, All Rights Reserved. Request academic re-use from www.copyright.com. All other uses, submit a request to [email protected]. For more inforrmation visit Asset & Logo Licensing.